Квалитет это проверка на прочность: детали и рекомендации
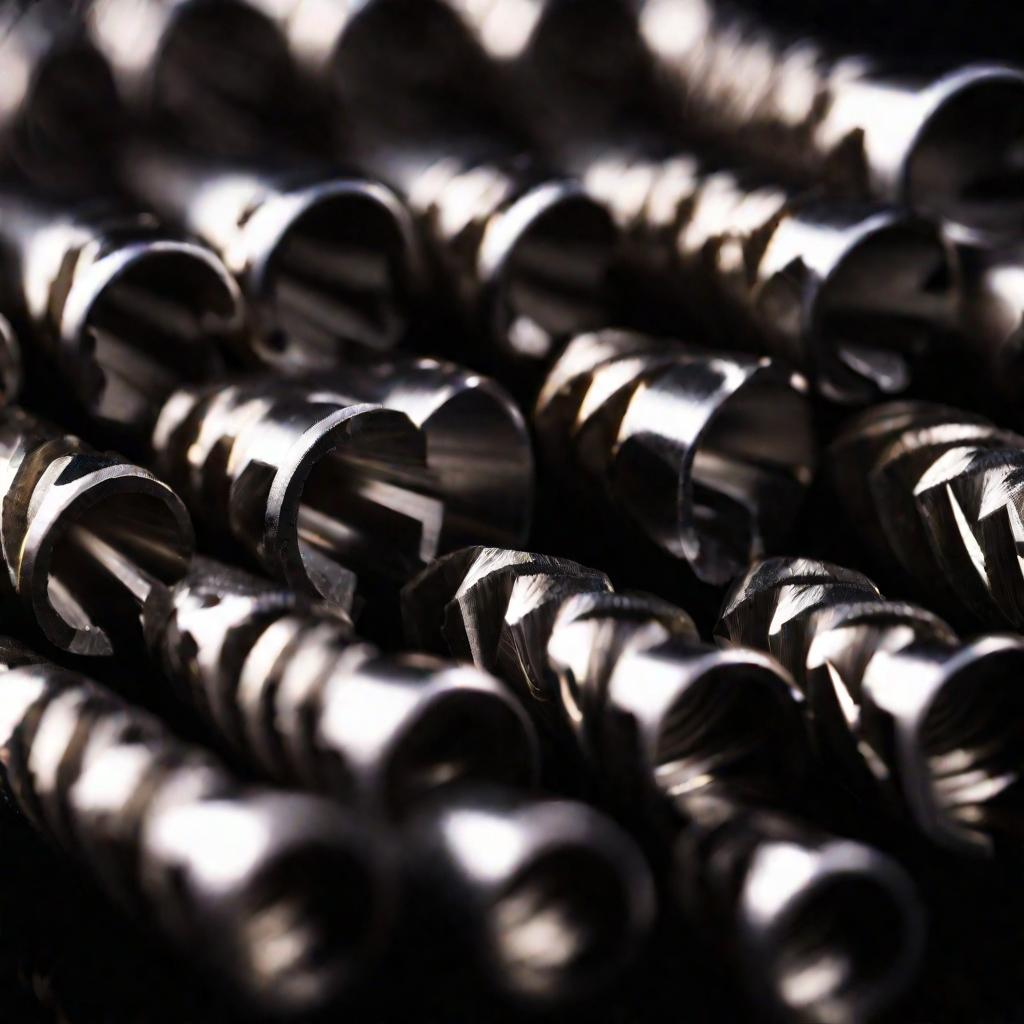
Квалитет - это не просто контроль точности, а настоящая проверка продукта на прочность. Давайте разберемся, как именно квалитет влияет на надежность и долговечность изделий.
История возникновения системы квалитетов в машиностроении

Причины появления квалитетов кроются в переходе от единичного производства к массовому. Раньше каждый мастер делал детали вручную, подгоняя их друг к другу. Когда заводы стали выпускать продукцию серийно, возник вопрос о взаимозаменяемости комплектующих. Чтобы деталь с одной фабрики подошла к изделию с другой, потребовались стандарты точности - квалитеты.
Развитие квалитетов шло вместе с прогрессом стандартизации и метрологии. Были разработаны система допусков и посадок, таблица стандартных квалитетов точности. Велось активное международное сотрудничество по унификации требований.
Основные вехи в истории квалитетов:
- 1760 год - осознание пользы разделения труда на производстве
- 1890 год - создание первых стандартов допусков в Германии
- 1938 год - принятие единой системы допусков и посадок (ЕСДП) в СССР
Физический смысл и определение квалитетов
Чтобы понимать суть квалитетов, нужно разобраться в таких понятиях, как:
- Размер детали
- Допуск на ее изготовление
- Посадка при соединении с другими деталями
Размер - это расстояние между двумя точками на поверхности детали. Допуск показывает, насколько можно отклоняться от заданного размера. А квалитет объединяет допуски с одинаковой точностью в группы.
Существует две системы квалитетов: вала и отверстия. В первом случае точность вала постоянна, а отверстия меняется. Во втором - наоборот. В машиностроении чаще применяют систему отверстия.
Всего установлено 20 стандартных квалитетов с обозначением 01, 0, 1, 2 и т.д. Чем выше номер - тем ниже точность детали. А значит, шире допуск на ее изготовление.
Квалитет показывает точность не только отдельной детали, но и всего изделия в целом.
Зависимость между квалитетом и эксплуатационными характеристиками
Квалитет это не просто абстрактная цифра. От точности деталей и их посадки зависят такие важные параметры, как:
- Виброустойчивость механизма
- Уровень шума при работе
- Износостойкость и срок службы
Чем выше квалитет, тем лучше эти характеристики. Например, повышение точности в 2 раза может снизить амплитуду вибраций станка примерно в 6-8 раз!2 Это серьезно влияет на качество обработки деталей.
Еще один важный фактор - температурные деформации. Чем больше допуск, тем сильнее геометрия детали меняется от нагрева или охлаждения. А значит, хуже работает весь механизм. Оптимальная рабочая температура у чугунных и полимербетонных станин тоже разная.
Материал станины | Допустимый температурный диапазон |
Серый чугун | +23°C ±2°C |
Кварцевое литье | от +18°C до +28°C |
Так что квалитет это еще и температурная стойкость! А значит, проверка на прочность в самых разных условиях эксплуатации.
Примеры испытаний станков с разными квалитетами
Чтобы наглядно оценить влияние квалитета, можно обратиться к результатам испытаний реальных станков. Так, при тестировании расточного станка на гранитной и чугунной станинах точность обработки отверстий на первой оказалась выше в 1,5-2 раза.
Также было проведено сравнение вертикально-фрезерного станка на синтетическом граните и его чугунного аналога. Оказалось, что вибрация бабки у гранитной модели в 1,6 раза ниже. А колебания самой станины - целых в 2,6 раза меньше!1

Требования к станкам с ЧПУ
Особенно важна высокая точность для станков с ЧПУ. Ведь все управление осуществляется программно, на основе заложенных геометрических параметров. Поэтому квалитет точности станин и бабок должен быть максимальным.
Дополнительное преимущество дают станины из минерального литья, так как они лучше гасят вибрации. А это напрямую влияет на точность позиционирования инструмента относительно обрабатываемой детали.
Требования к измерительным инструментам
От квалитета напрямую зависит и точность контрольно-измерительных инструментов: штангенциркулей, микрометров, индикаторов часового типа.
Нестабильность размеров с течением времени здесь недопустима. Поэтому корпус таких приборов делается из специальных антиусадочных сплавов, например на основе инвара или нержавеющей стали.
Квалитет сверл и другого режущего инструмента
Оптимальная точность нужна не только для корпусных деталей, но и для режущего инструмента. К примеру, класс точности сверл напрямую влияет на квалитет обрабатываемого отверстия:
- Сверла А1 - для 10-13 квалитетов точности
- Сверла В1 - для 14 квалитета точности
- Сверла В - для 15 квалитета точности
Значит, выбирая квалитет точности для сверла, мы задаем будущий квалитет детали! То же самое касается фрез, зенкеров, разверток и другого металлорежущего инструмента.
Похожие статьи
- Парные и непарные, звонкие и глухие, мягкие и твердые согласные звуки в русском языке
- Подготовка к исповеди. Список грехов для исповеди
- Какие бывают предложения по цели высказывания и по интонации? Виды предложений по цели высказывания
- Белоруссия или Беларусь: как правильно говорить и писать?
- Расположение органов у человека (фото). Внутренние органы человека: схема расположения
- Характеристика Льва-женщины. Знак Зодиака Лев: описание
- История Кёсем Султан: биография, правление и интересные факты